Bereit für Industrie 4.0 mit TR-Electronic
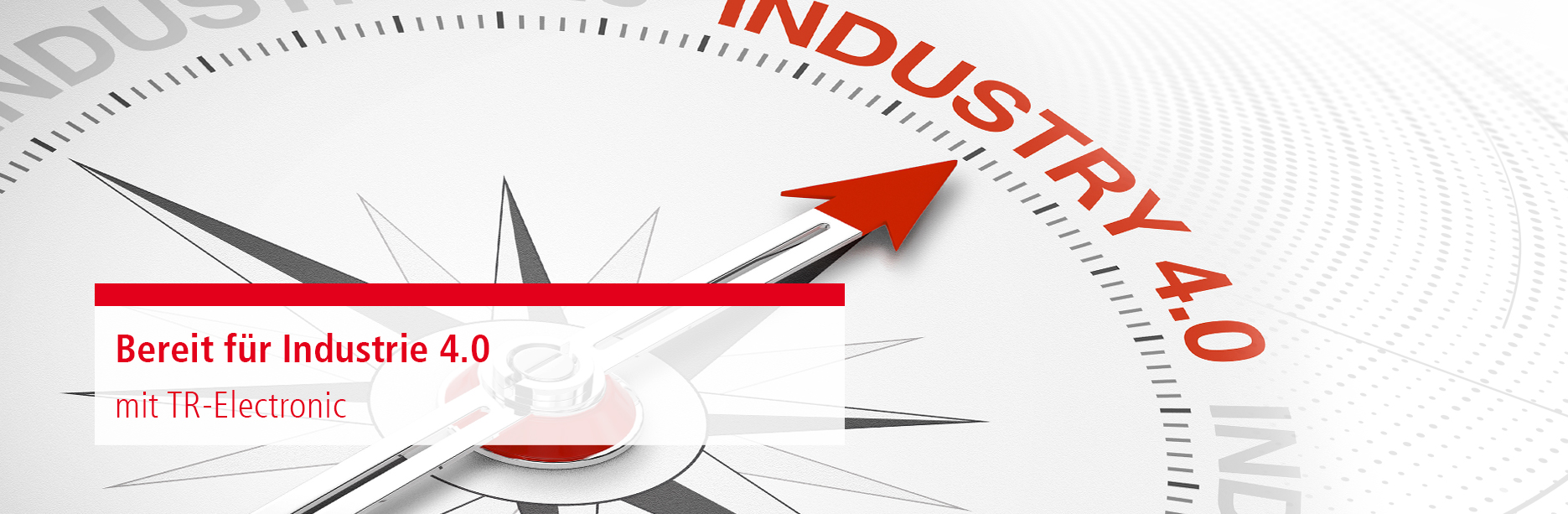
Die durchgehende Vernetzung und offene Kommunikation zwischen Anlagen sind die Triebfeder für Industrie 4.0. Die steigende Individualisierung von Produkten und die Umsetzung von zusätzlichen Funktionen von Produktionsanlagen bei der gleichzeitigen Forderung nach vertretbaren Preisen verlangen nach intelligenten, adaptiven, miteinander kommunizierenden Produktionssystemen. Direkter Austausch von Rezeptur- und Prozesssteuerungsdaten, dynamische Anpassung von Fertigungsprozessen und Materialfluss sowie eine produktbegleitende Dokumentation sichern hohe Flexibilität, um die vielfältigen Wünsche von Anwendern zu erfüllen und gleichzeitig effizient zu produzieren.
- TR-Sensoren als Quelle für „Big-Data“-Anlagenanalyse
- Prozess- und Zustandsdaten für die Weiterverarbeitung in übergeordneten Systemen
- Bewegungsdaten (Drehzahlbereiche, Gesamtumdrehungszahl)
- Kommunikationsdaten und Ausfälle
- Spannungsversorgung und Ausfälle
- Umweltbedingungen (Kerntemperatur des Messsystems…)
- Nutzung asynchroner Datenkanäle in Feldbus und Industrial Ethernet.
Hersteller von Maschinen und Anlagen versuchen, über eine Vielzahl erfasster Prozessbegleitdaten, den Zustand der Anlage zu analysieren und so unerwünschte Zustände wie fehlerhafte Produktion oder Anlagenstillstand zu vermeiden.
Dazu sammeln Maschinen- und Anlagensteuerungen viele Daten, die vordergründig nicht für den eigentlichen Prozess entscheidend sind und werten diese mit Methoden von „Big Data“ aus. Dabei geht es im Allgemeinen seltener um den Zustand des Drehgebers selbst: Einbauen, anschließen, vergessen. Vielmehr interessiert der Zustand von grundsätzlich verschleißbehafteten Komponenten und Bauteilen.
Ein Beispiel:
Für einen Positioniervorgang ist eigentlich nur die erreichte Position interessant – sie ist als Rückführungsgröße der zentrale Bestandteil der Positionsregelung. Für die Lebensdauer verbauter Antriebskomponenten (Lager, Wellen, Motoren) dürfte jedoch interessant sein, wie häufig, mit welchen Achsdrehzahlen und welchem Moment positioniert wurde. Auskunft über Häufigkeit und Drehzahl liefert ein Drehgeber, das Moment wird vom Umrichter aus den Stromwerten ermittelt. Führt ein übergeordnetes System diese Daten zusammen, ergibt sich ein umfassendes Zustandsbild der Anlage. Ebenso könnte es interessant sein, kurzzeitige Ausfälle in der Kommunikation zu einzelnen Sensoren in ihrer Häufigkeit zu erfassen, um einem sich entwickelnden Kabelbruch in einer Schleppkette zu erahnen, bevor das betreffende Anlagenmodul unerwartet ausfällt. Die Möglichkeiten sind nahezu unbegrenzt. Im Zusammenspiel von Sensorik, Steuerungsebene, Datenspeicherung und Auswertung gewinnen Nutzer und Konstrukteure von Maschinen und Anlagen ein umfassendes Bild.
Dreh- und Lineargeber von TR-Electronic, insbesondere wenn sie mit Feldbus- und Industrial Ethernet Schnittstellen ausgelegt sind, erfassen intern weitaus mehr Daten als die für den Prozess primär entscheidenden Positions- und Geschwindigkeitswerte. Dazu zählen je nach Schnittstelle und Produktfamilie unter anderem Informationen über die Qualität der Spannungsversorgung, der Zustand der Netzwerkverbindung, Drehzahlbereiche über Zeit…
Planer und Errichter, häufig auch nur die Betreiber können die Gesamtheit der Daten verschiedener Anlagen und Maschinen erfassen und statistisch zielgerichtet auswerten. TR-Electronic bietet in den aktuellen Sensorik-Familien eine große Auswahl von Kenndaten, die für eine Beurteilung des Gesamtzustandes herangenzogen werden können und stellt sie über standardisierte Kommunikationswege im Industrial Ethernet oder im traditionellen Feldbus zur Verfügung.
Die erweiterten Sensordaten in den Dreh- und Lineargebern von TR-Electronic können, mit anderen Daten sinnvoll zusammengeführt und ausgewertet, wertvolle Informationen über Maschinen und Anlagen liefern.